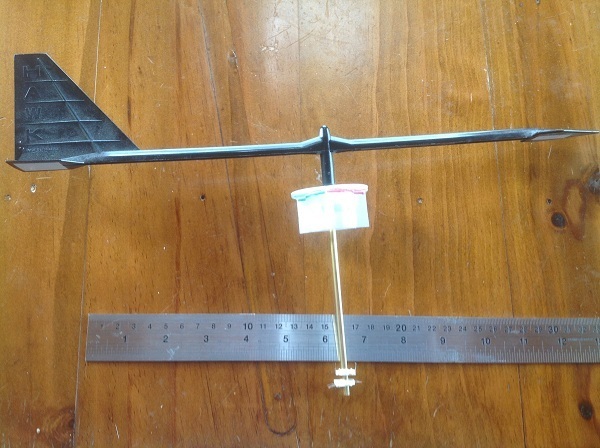
Wind Direction Indicator
By Dermot Tynan, over 12 years ago.
Now that the hull is looking solid, it's time to start thinking again about the wind direction indicator. It is possible to detect wind speed by using an ultrasonic sensor and receiver, and measuring the delay between the two. You need to account for temperature changes and gusts can cause issues, but it is fairly reliable and has no moving parts. Generally, you use two transducers offset by a distance of perhaps 20cm for the North/South computation, and another pair in the East/West direction. I think if we were using a larger hull, such as a 4m boat, this would be a good plan. But, for the 2.4m (or the 1.2m) boat, it's just too big and awkward. Also, this jury is undecided about how well they would work, over the long haul.
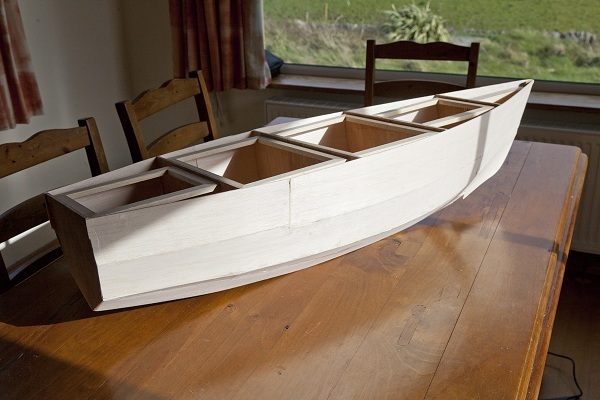
Hull 001 is almost ready for fibreglass
By Dermot Tynan, over 12 years ago.
After applying 3/32" balsa wood to the bulkheads and transom, the hull is starting to look like a real boat!
You can clearly see the deck support frames now. They are 6mm below the sheer line, to allow for 6mm exterior (or marine) ply deck pieces. But first, the balsa needs to be sanded and patched a bit. Also, the 3 or 4 layers of chopped strand matt need to be applied. When it is finished, the balsa wood will be completely enclosed in fibreglass. This is a standard "sandwich" construction. The balsa adds a layer of strength (believe it or not!) to the two layers of glass either side. It is similar to the central section of an I-beam or girder in that it separates the two outer layers and means that the bend radius is increased. Or at least, that's my understanding of it...
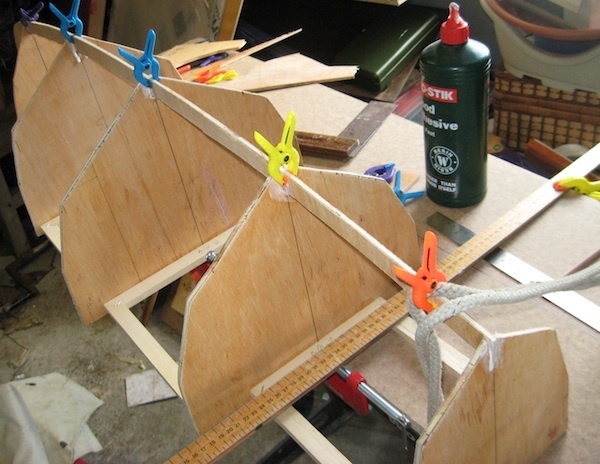
The keel is attached.
By Dermot Tynan, over 12 years ago.
After much sanding and polishing of the keelson, and the frames for the hatches and top deck, the hull is starting to take shape.
The bulkheads are cut from 6mm exterior grade plywood. The wood which resembles a picture frame is pine, and it is used to hold the bulkheads and transom into a square position, and to provide additional strength to the hull. Eventually those frames will be covered over by 6mm ply on the deck.
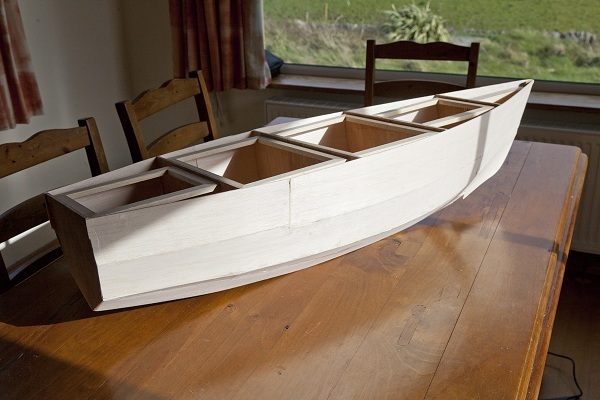
Cutting out the Bulkheads.
By Dermot Tynan, over 12 years ago.
A slight change from the version of the hull from The hull starts to take shape.; the hull height from the base of the hull to the deck (not including the keel) was 180mm. As I started to look at cutting bulkheads and the transom, it struck me that the hull is quite shallow. It looks fine from DelftSHIP but that's a low freeboard.
The beam of the boat is around 360mm, which is twice that depth. The original intent was to create a hull which wasn't too "beam-y" but that's a 2:1 aspect ratio. I decided to increase the hull height by 50%. Luckily, DelftSHIP will scale your drawing in any or all of the three vertices. So, five minutes later, and we have a new hull with a 270mm depth.
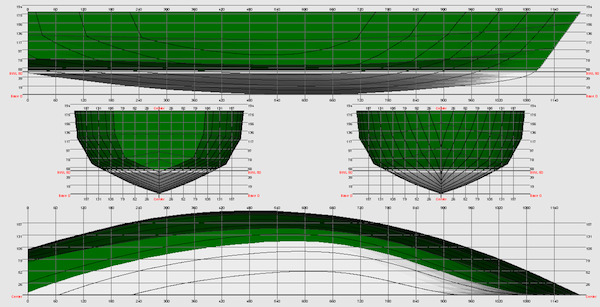
The hull starts to take shape.
By Dermot Tynan, over 12 years ago.
On Henry's advice, the round hull of earlier designs has been discarded in favour of a hard-chined hull. We were originally planning a fibreglass hull from a round mould. The complexities of first producing a "plug" and preparing a mould from the plug, not to mention having to then fibreglass the hull itself, are quite involved. Henry suggested hard chines an 6mm marine ply for the construction, and a light bulb lit up.
Upcoming Missions
- Galway Bay Loop, Waiting for Vessel Availability
Search
Recent Posts
- May 2023 (1 post)
- April 2023 (1 post)
- March 2023 (1 post)
- February 2023 (2 posts)
- March 2022 (3 posts)
- March 2021 (1 post)
- August 2020 (1 post)
- May 2019 (1 post)
- April 2018 (1 post)
- November 2017 (1 post)
- April 2017 (1 post)
- November 2016 (1 post)
- September 2016 (1 post)
- August 2016 (1 post)
- January 2014 (2 posts)
- October 2013 (7 posts)
- September 2013 (1 post)
- August 2013 (3 posts)
- June 2013 (3 posts)
- May 2013 (4 posts)
- April 2013 (3 posts)
- March 2013 (9 posts)
- February 2013 (8 posts)