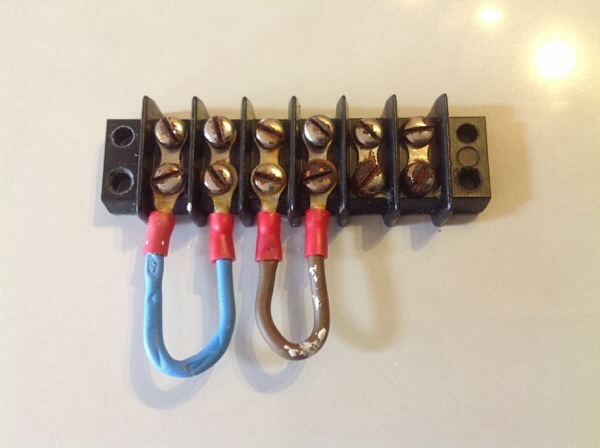
First signs of weathering.
By Dermot Tynan, about 12 years ago.
In order to test the spiffy, new Wind Direction Indicator mentioned in The Marvel of 3D Printing..., I assembled the mechanical components (without the potentiometers) and mounted it outside. As we live in a wind-swept area, with a high concentration of sea salt in the air, it was a useful test of how the system would perform. What I couldn't test was the effect of high temperature/humidity in a salt-water environment. To do that, I'd have to move to the Caribbean (which seems like a good idea, given the Irish summer we've had so far!).
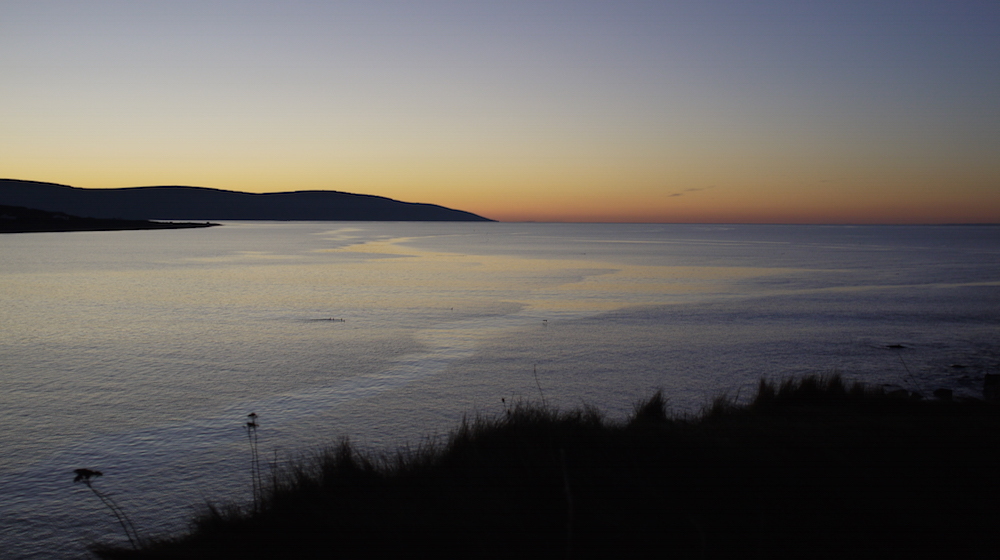
Mission 001 - Galway Bay
By Dermot Tynan, about 12 years ago.
As the hull is now watertight, and we're mere weeks away from having a sealed hull with keel and rig, it's OK to start looking at actually getting this thing to sail.
Up until now, I've been somewhat obsessed with getting the physical aspects of the boat to a certain juncture. The reasoning is simple; until there's a boat, all of this other stuff is just a waste of time. Well, now there's a boat...
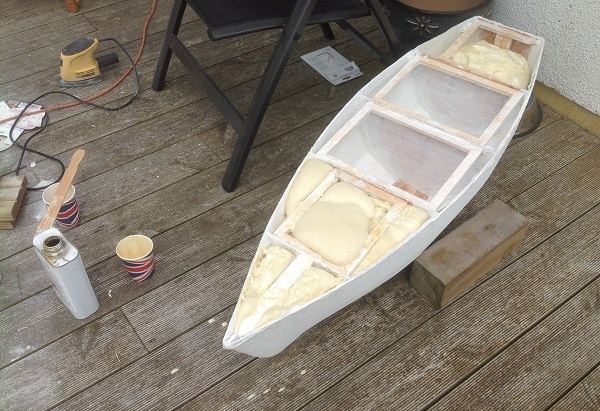
Almost There...
By Dermot Tynan, about 12 years ago.
After a lot of sanding, fibreglassing and applying resin, the hull is looking like it is ready for salt water. As you can see from an earlier post (Hull 001 is almost ready for fibreglass), the hull is formed by gluing thin balsa strips to the plywood bulkheads. These strips give the hull its shape, and also provide a modicum of structural integrity. On the outside of this balsa, are 3 layers of 300g chopped-strand matt, finished with a layer of fibreglass tissue. Each layer is impregnated with polyester resin. Likewise, the inside of the hull is coated with two layers of 300g CSM. Ultimately, all of the balsa wood is covered with at least two layers of fibreglass, which is a good idea because fibreglass on its own isn't that strong, and is susceptible to rotting, particularly in warm, humid waters.
Upcoming Missions
- Galway Bay Loop, Waiting for Vessel Availability
Search
Recent Posts
- May 2023 (1 post)
- April 2023 (1 post)
- March 2023 (1 post)
- February 2023 (2 posts)
- March 2022 (3 posts)
- March 2021 (1 post)
- August 2020 (1 post)
- May 2019 (1 post)
- April 2018 (1 post)
- November 2017 (1 post)
- April 2017 (1 post)
- November 2016 (1 post)
- September 2016 (1 post)
- August 2016 (1 post)
- January 2014 (2 posts)
- October 2013 (7 posts)
- September 2013 (1 post)
- August 2013 (3 posts)
- June 2013 (3 posts)
- May 2013 (4 posts)
- April 2013 (3 posts)
- March 2013 (9 posts)
- February 2013 (8 posts)