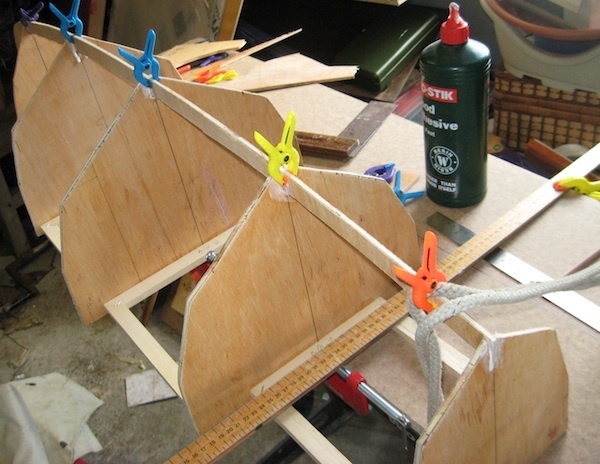
The keel is attached.
By Dermot Tynan, over 12 years ago.
After much sanding and polishing of the keelson, and the frames for the hatches and top deck, the hull is starting to take shape.
The bulkheads are cut from 6mm exterior grade plywood. The wood which resembles a picture frame is pine, and it is used to hold the bulkheads and transom into a square position, and to provide additional strength to the hull. Eventually those frames will be covered over by 6mm ply on the deck.
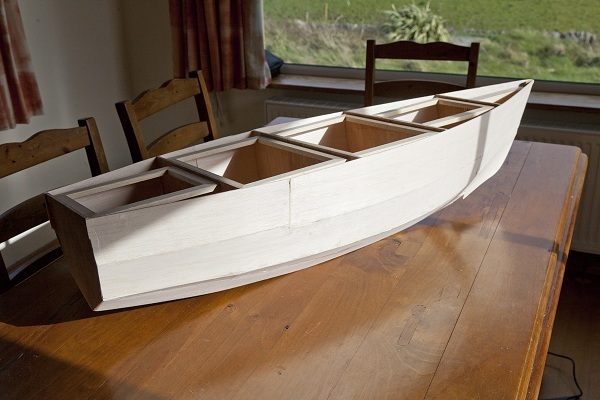
Hull 001 is almost ready for fibreglass
By Dermot Tynan, over 12 years ago.
After applying 3/32" balsa wood to the bulkheads and transom, the hull is starting to look like a real boat!
You can clearly see the deck support frames now. They are 6mm below the sheer line, to allow for 6mm exterior (or marine) ply deck pieces. But first, the balsa needs to be sanded and patched a bit. Also, the 3 or 4 layers of chopped strand matt need to be applied. When it is finished, the balsa wood will be completely enclosed in fibreglass. This is a standard "sandwich" construction. The balsa adds a layer of strength (believe it or not!) to the two layers of glass either side. It is similar to the central section of an I-beam or girder in that it separates the two outer layers and means that the bend radius is increased. Or at least, that's my understanding of it...
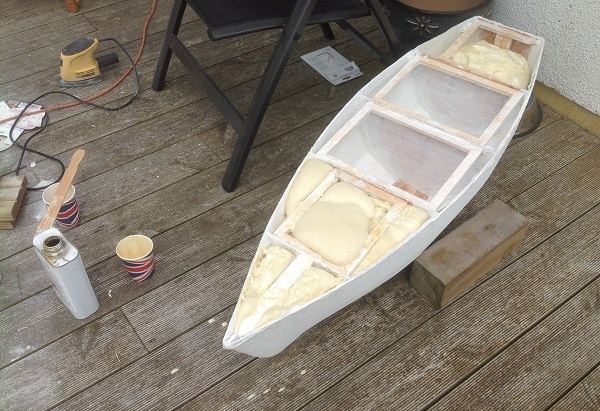
Almost There...
By Dermot Tynan, about 12 years ago.
After a lot of sanding, fibreglassing and applying resin, the hull is looking like it is ready for salt water. As you can see from an earlier post (Hull 001 is almost ready for fibreglass), the hull is formed by gluing thin balsa strips to the plywood bulkheads. These strips give the hull its shape, and also provide a modicum of structural integrity. On the outside of this balsa, are 3 layers of 300g chopped-strand matt, finished with a layer of fibreglass tissue. Each layer is impregnated with polyester resin. Likewise, the inside of the hull is coated with two layers of 300g CSM. Ultimately, all of the balsa wood is covered with at least two layers of fibreglass, which is a good idea because fibreglass on its own isn't that strong, and is susceptible to rotting, particularly in warm, humid waters.
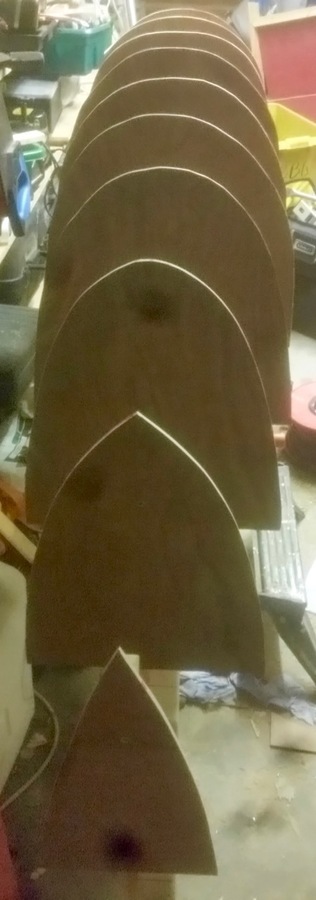
Hull 002
By Dermot Tynan, almost 9 years ago.
I have discussed the hull construction process in earlier posts, which you can find via the above search bar. To recap, you take the hull design and "loft" the shape of each section or bulkhead, from the drawing. You then cut this out of 6mm marine ply (or equivalent), mount each of the stations onto a strongback, and now you have something which forms the shape.
I also need to add a keelson to the picture. A keelson is a long, keel-like piece of wood which runs from stem to stern, connecting the bulkheads. I cut one already but it turned out to be too short due to a miscalculation on my part. Generally I cut a thin (about 2cm wide) outline of the keel of the boat, from a sheet of ply.
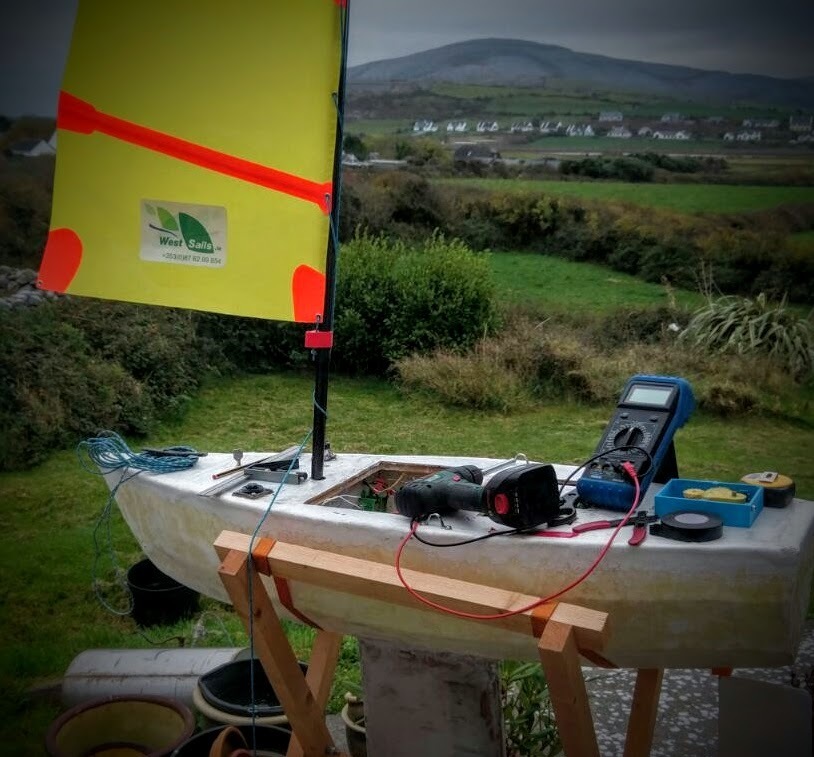
Impending Launch.
By Dermot Tynan, almost 9 years ago.
Hull #002 is coming along, slowly. The stations are mounted on the strongback and I've been double-checking the alignment. I have time to do this because 1/32nd inch balsa wood is hard to come by, and because I haven't cut the keelson yet. Well, I have, but I need to re-cut it. The original was cut to the wrong profile.
While the work on hull 2 continues, I've been using Hull #001 to test out aspects of the boat design and control systems. In fact, I am very close to launching the hull…
Upcoming Missions
- Galway Bay Loop, Waiting for Vessel Availability
Search
Recent Posts
- May 2023 (1 post)
- April 2023 (1 post)
- March 2023 (1 post)
- February 2023 (2 posts)
- March 2022 (3 posts)
- March 2021 (1 post)
- August 2020 (1 post)
- May 2019 (1 post)
- April 2018 (1 post)
- November 2017 (1 post)
- April 2017 (1 post)
- November 2016 (1 post)
- September 2016 (1 post)
- August 2016 (1 post)
- January 2014 (2 posts)
- October 2013 (7 posts)
- September 2013 (1 post)
- August 2013 (3 posts)
- June 2013 (3 posts)
- May 2013 (4 posts)
- April 2013 (3 posts)
- March 2013 (9 posts)
- February 2013 (8 posts)