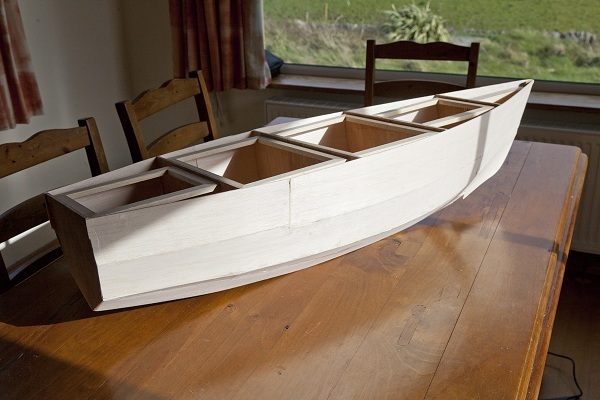
Cutting out the Bulkheads.
By Dermot Tynan, over 12 years ago.
A slight change from the version of the hull from The hull starts to take shape.; the hull height from the base of the hull to the deck (not including the keel) was 180mm. As I started to look at cutting bulkheads and the transom, it struck me that the hull is quite shallow. It looks fine from DelftSHIP but that's a low freeboard.
The beam of the boat is around 360mm, which is twice that depth. The original intent was to create a hull which wasn't too "beam-y" but that's a 2:1 aspect ratio. I decided to increase the hull height by 50%. Luckily, DelftSHIP will scale your drawing in any or all of the three vertices. So, five minutes later, and we have a new hull with a 270mm depth.
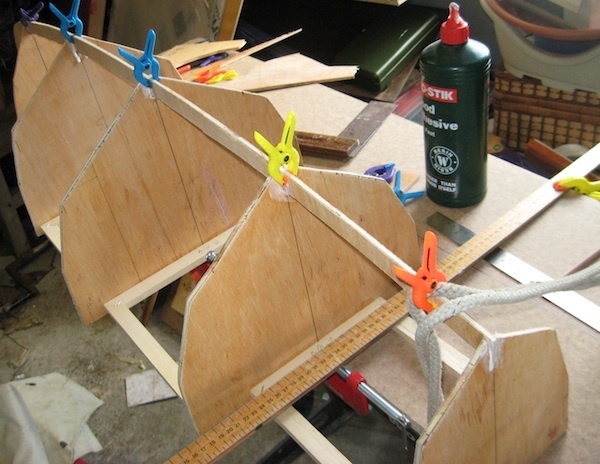
The keel is attached.
By Dermot Tynan, over 12 years ago.
After much sanding and polishing of the keelson, and the frames for the hatches and top deck, the hull is starting to take shape.
The bulkheads are cut from 6mm exterior grade plywood. The wood which resembles a picture frame is pine, and it is used to hold the bulkheads and transom into a square position, and to provide additional strength to the hull. Eventually those frames will be covered over by 6mm ply on the deck.
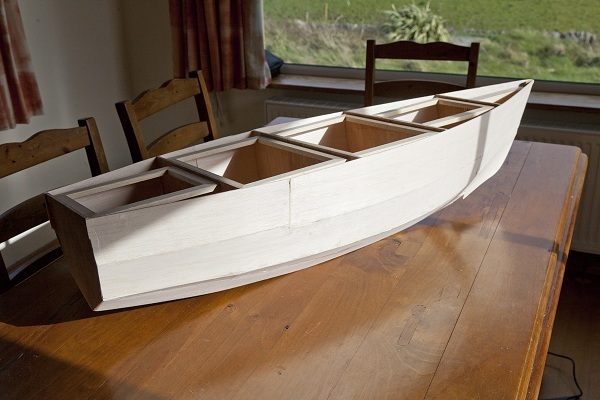
Hull 001 is almost ready for fibreglass
By Dermot Tynan, over 12 years ago.
After applying 3/32" balsa wood to the bulkheads and transom, the hull is starting to look like a real boat!
You can clearly see the deck support frames now. They are 6mm below the sheer line, to allow for 6mm exterior (or marine) ply deck pieces. But first, the balsa needs to be sanded and patched a bit. Also, the 3 or 4 layers of chopped strand matt need to be applied. When it is finished, the balsa wood will be completely enclosed in fibreglass. This is a standard "sandwich" construction. The balsa adds a layer of strength (believe it or not!) to the two layers of glass either side. It is similar to the central section of an I-beam or girder in that it separates the two outer layers and means that the bend radius is increased. Or at least, that's my understanding of it...
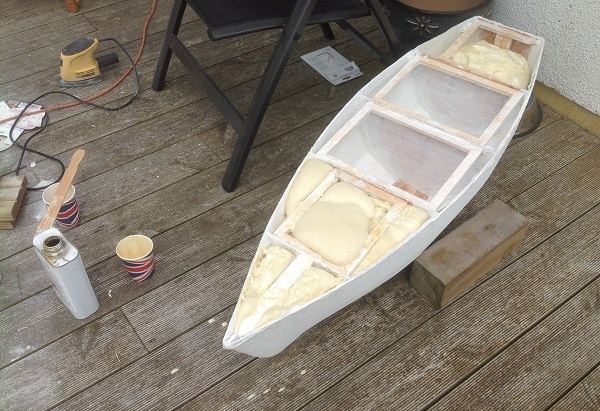
Almost There...
By Dermot Tynan, about 12 years ago.
After a lot of sanding, fibreglassing and applying resin, the hull is looking like it is ready for salt water. As you can see from an earlier post (Hull 001 is almost ready for fibreglass), the hull is formed by gluing thin balsa strips to the plywood bulkheads. These strips give the hull its shape, and also provide a modicum of structural integrity. On the outside of this balsa, are 3 layers of 300g chopped-strand matt, finished with a layer of fibreglass tissue. Each layer is impregnated with polyester resin. Likewise, the inside of the hull is coated with two layers of 300g CSM. Ultimately, all of the balsa wood is covered with at least two layers of fibreglass, which is a good idea because fibreglass on its own isn't that strong, and is susceptible to rotting, particularly in warm, humid waters.
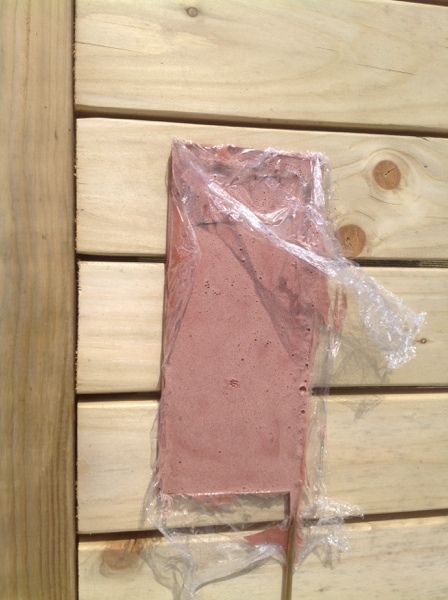
The new rudder
By Dermot Tynan, almost 12 years ago.
Thanks go to Colman Corrigan for designing and building the keel and rudder. The keel follows the traditional NACA shape, with a rounded leading-edge, tapering off to a narrow trailing edge. It is approximately a 6318 shape, with the maximum width being about 36% of the length of the cross-section. Overall, the keel is coming in at about 750mm from hull to the end of the bulb, and about 240mm from front to back. That's a 3:1 aspect ratio.
Upcoming Missions
- Galway Bay Loop, Waiting for Vessel Availability
Search
Recent Posts
- May 2023 (1 post)
- April 2023 (1 post)
- March 2023 (1 post)
- February 2023 (2 posts)
- March 2022 (3 posts)
- March 2021 (1 post)
- August 2020 (1 post)
- May 2019 (1 post)
- April 2018 (1 post)
- November 2017 (1 post)
- April 2017 (1 post)
- November 2016 (1 post)
- September 2016 (1 post)
- August 2016 (1 post)
- January 2014 (2 posts)
- October 2013 (7 posts)
- September 2013 (1 post)
- August 2013 (3 posts)
- June 2013 (3 posts)
- May 2013 (4 posts)
- April 2013 (3 posts)
- March 2013 (9 posts)
- February 2013 (8 posts)